Imagining the Unimaginable: Golden Eagle Develops World’s First 3D-Printed Airless Basketball for Wilson
Wed, 06/12/2024 - 02:19pm | By: Karelia Pitts
“How many new ways to make a basketball can you come up with?”
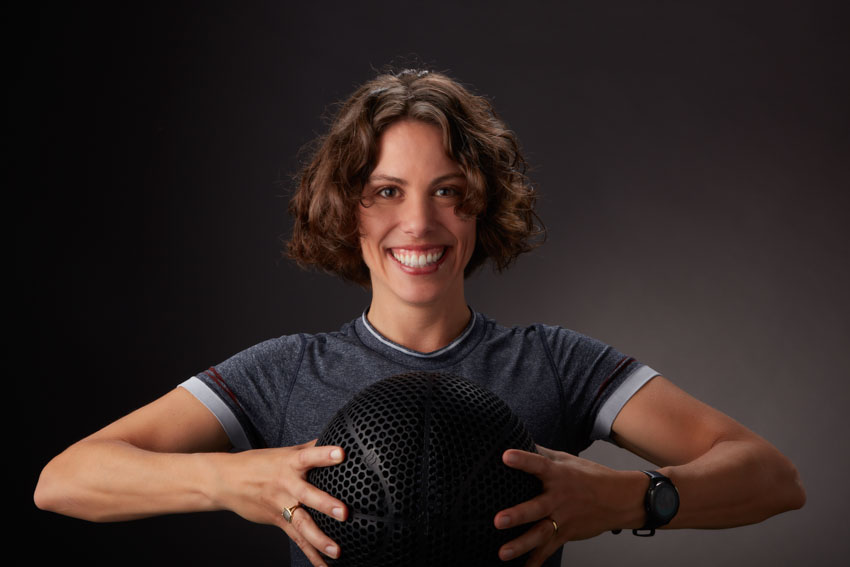
In 2018, Dr. Nadine Lippa was tasked with this challenge on her first day as principal materials engineer for Wilson Sporting Goods. The concept instantly set her thoughts in motion as she imagined all the possibilities.
Although her answer at the time was “I currently know of zero ways,” an uncontrollable grin stretched across her face. She knew she was in the right place to learn and push her limits. The charge to reinvent the basketball for Wilson could have intimidated her, but Nadine was too busy chasing down leads to let doubts hold her back.
“I love exposure to new things and approaching a topic with a beginner’s mind. When presented with a problem, I enjoy the freedom to search the world for uncommon and sometimes unimaginable solutions,” Nadine described. “Some of that comes naturally for me, and some of it comes from my experience at Southern Miss.”
Southern Miss Made
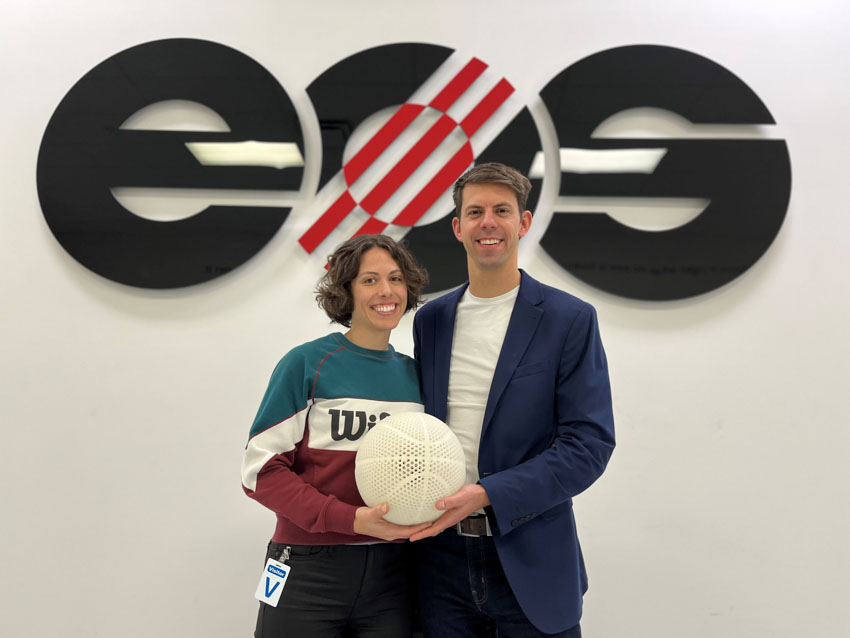
A 2008 dual-major graduate of Carnegie Mellon University in materials science and biomedical engineering, Nadine was an avid multi-sport athlete seeking a career that combined her interests in sports and engineering. A faculty mentor suggested the Ph.D. program in sport and high-performance materials at The University of Southern Mississippi (USM) and connected her with a recent Carnegie Mellon alumnus, Dave Krzeminski, who had successfully completed his first year in the program.
“Pretty quickly into my tour at USM, I knew I wanted to come here because everyone was so friendly, knowledgeable and incredibly passionate about what they were doing. The faculty and students I talked with had a very clear understanding of their ‘why,’ and I got a sense that I could craft my own trajectory here. It was exhilarating!”
The program offered a multidisciplinary degree through the collaboration of USM’s School of Polymer Science and the School of Human Performance and Recreation. Students explored polymer science and human subject research to improve sports equipment, ranging from performance to injury preventative devices. Under the guidance of Dr. James Rawlins (professor of polymer science and engineering) and Dr. Trent Gould (professor of kinesiology), Nadine was a sponge.
“Being co-advised by two accomplished scientists in contrasting fields allowed me to learn from the best of both arenas. Balancing their different ways of seeing things, understanding the unique value each one brings, and finding a way to marry the two definitely set me up for success in the professional world.
At Wilson, I work with a rich variety of professionals who are experts in their respective areas. I’m constantly receiving feedback, but sometimes the comments are conflicting. For example, there are people who pick up our 3D-printed basketball and say it’s too light while others say it’s too heavy. Some think it’s too big, but others think it’s too small. My job requires me to collect the data, but also confidently and continuously balance diverse perceptions as inputs and use the resources at my disposal to produce a successful output. I’m so thankful that Southern Miss gave me practice and a strong foundation for navigating that kind of fast-paced, dynamic environment.”
Nadine’s dissertation work was instrumental in honing these skills. Although she admired the research Drs. Rawlins and Gould were each conducting, Nadine knew she wanted to forge her own path. Narrowing down the scope of her project was the first major hurdle.
“I remember filling an entire sheet with ideas about potential research topics and pitching those to Dr. Rawlins. I was gushing about each of the thoughts I had jotted down throughout my first year in the program when he looked at me and simply said ‘Yes.’ I was confused because I had just posed dozens of potential research questions. He explained, ‘I can tell you have a lot of passion, and whatever you want to do, we’ll do it.’ I felt so energized by the support he and Dr. Gould generously provided and the confidence in me they demonstrated.”
The invigorating mentorship Nadine received from her co-advisors and faculty empowered her to explore her curiosities and chase her loftiest goals. USM also provided Nadine with the opportunity to get to know Dave, her fellow Carnegie Mellon grad turned Golden Eagle. A deep friendship and mutual respect developed during their long hours in the lab, and the Southern Miss sweethearts got engaged in 2015.
The same year, Nadine secured a visiting research fellowship at Deakin University in Australia, where she gained access to rare equipment. Using motion capture and a force-plate instrumented treadmill, she measured gait and forces from female runners wearing traditional and minimalist running shoes and replicated the forces in a mechanical testing machine to monitor how the shoes degraded. She then asked the participants to return to the lab and run in the aged shoes a second time to understand how broken-down shoes in turn changed how they ran. This work contributed to her doctoral dissertation titled, “Energy Management Mechanisms Employed at the Human-Material Interface of Traditional and Minimalist Running Shoe Foams.”
She focused on running biomechanics and shoe polymeric materials (i.e., midsole foam) to quantify service life, increase material performance and ultimately decrease the incidence of common overuse running injuries. The challenging and rewarding dissertation process solidified her interest in working autonomously on complex, ambiguous problems like the ones she would one day be exposed to at Wilson.
Entering the Industry
While conducting research for her dissertation, Nadine was invited to present at the International Sports Engineering Association conference in Sheffield, England. Hoping to stand out among her doctoral student peers, Nadine was pleasantly surprised when she was awarded the best presentation overall, representing the top recognition for both students and faculty.
The director of innovation for Adidas happened to be in attendance, and he was so impressed by Nadine’s research and presentation skills that he offered her a post-doctoral internship developing future sport products and materials at Adidas’ headquarters in Herzogenaurach, Germany.
Next, she landed a job as senior engineer – Ph.D. materials scientist for Gentex Corporation, where she worked on developing forthcoming technologies for military, sport and general use protective and functional eyewear. That is where she caught the attention of Wilson Sporting Goods.
Developing the Airless Basketball
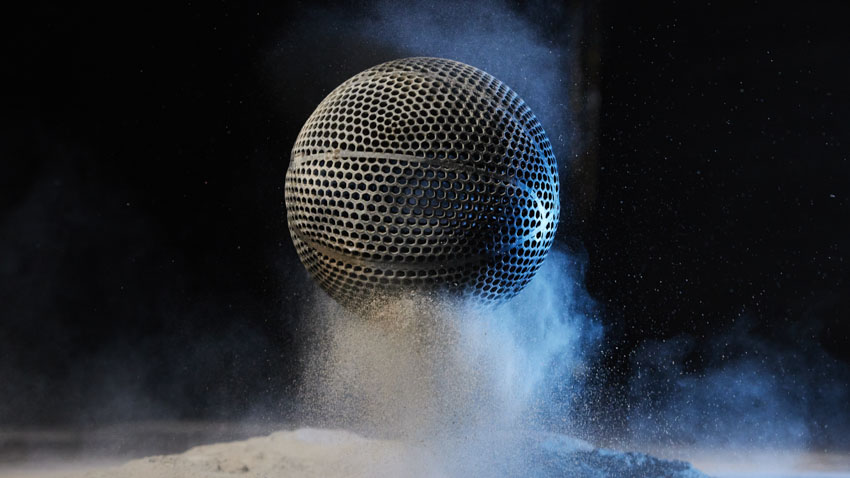
From ideation to prototype, it took Nadine and her team at Wilson five years to find the right combination of material properties and mechanical design needed for the airless basketball. While testing and retesting every method imaginable, Nadine became the self-proclaimed “ugly sample lady” in the office. A pile of unsuccessful attempts that either broke or failed to bounce began to stack up on her desk before she finally experienced a breakthrough.
“3D printing was one of the first manufacturing methods we considered for the airless basketball in 2018, but the material properties just weren’t where we needed them to be at the time. Still, we learned a lot through experimentation with various additive methods as the technology matured and more elastomers became available. Ultimately, we achieved success with EOS, a company we’d approached early on.”
EOS provides responsible manufacturing solutions via industrial 3D printing technology to manufacturers around the world. Their capabilities evolved tremendously from 2018 to 2021, making additive manufacturing the sole technology on Earth that could finally bring the airless prototype to life.
The partnership was sweetened for Nadine when her husband, Dave, was hired by EOS and joined the project team. Due to strict company confidentiality, her lips had been completely sealed for the entirety of the project to that point. At home, they put family first and avoided talk from the office. With their shared skills and interest in sport and high-performance materials, the couple was fortunate to be able to collaborate on a project this special.
“The Airless Prototype utilizes advanced lattice geometry enabled by 3D printing to perform just like a traditional game ball. General Lattice, a computational design and digital manufacturing company, helped develop our lattice design, which translated into a digital file that can be easily read by EOS’ 3D printers. The result was revolutionary for us, and I’m pretty sure I cried the first time we produced a sample that successfully bounced like a basketball.”
When asked to explain the steps of manufacturing the Airless Prototype, Nadine describes, “What happens is there’s a powder bed that’s swept across, then a laser almost Etch-a-Sketches the pattern in two dimensions. As this process iterates over and over, you end up with a three-dimensional ball. We remove that powder from the ball, then seal and dye it using a smoothing technique developed by a company called DyeMansion. Dye penetrates and reacts with the polymeric surface before we send the ball to our NBA test facility in Ada, Ohio, where they put it through rigorous testing.”
She may make the process sound simple and straightforward, but the concept is groundbreaking for the industry.
“To witness years of work coming together into one specific product and to think back on all the decisions made up to this point is such an incredible and life-changing experience for me. As innovation manager for Wilson, my job is to push boundaries for the brand and change perceptions. I’m so honored to have been able to lead this first of many projects that has the potential to reach that goal and transform sports.”
NBA Reveal
Nadine was finally able to share her team’s creation with the world on February 18, 2023, during the NBA Slam Dunk Contest featuring Kenyon “K.J.” Martin Jr. of the Houston Rockets. Although he was initially skeptical about whether a basketball with holes could bounce and feel like the ball he is familiar with, he quickly took a liking to the Airless Prototype.
In weight, size and bounce, the 3D-printed ball nearly matches the performance specifications of a standard basketball without requiring inflation. Eight panel-like lobes mimic a traditional leather ball but feature a sleek 3D-printed lattice instead of pebbled leather. The surface of the ball consists of small hexagonal holes which allow air to pass through freely.
While Nadine and her colleagues eagerly watched from courtside, K.J. gripped, dribbled and dunked the Airless Prototype in style. The crowd roared!
“The rush of the dunk contest was insane! I was so excited but also a little scared because expectations were so high. We really didn’t know how people were going to receive it, but the experience turned out to be so gratifying and validating. The feelings that come from seeing others marvel at something you worked tirelessly to create are truly indescribable.”
On to the Next Challenge
“The genesis of why we’re doing this work at Wilson stretches beyond just making a cool looking basketball. Sustainability drives many of our motivations as we explore the possibilities of being able to manufacture balls in North America. Overall, we want to find innovative solutions that reduce our impact and improve our products.”
Following the reveal of the Wilson Airless Prototype, Nadine’s challenge shifted from creating one 3D-printed basketball to figuring out how to mass produce them.
“While working on my Ph.D., I learned that at some point there is no expert to turn to. You have to become the expert. Southern Miss taught me to order off the menu, trust my instincts and come up with my own ideas. Those skills have become invaluable to me.”
On February 16, 2024, a year after the prototype’s NBA unveiling, Nadine and her team celebrated the Airless Gen1 going to market with the help of manufacturing partner SNL Creative. In under two hours, Wilson sold out of the exclusive release ball that was 100 percent made in America. Offered in black, natural and brown color options, the limited run of Airless Gen1 balls retailed for $2,500 each.
“I feel really grateful for the years I spent at USM and that Wilson is investing in this type of project that really pushes the envelope on what is possible. They both took a chance on me… brought in somebody who didn’t know much and let her learn. I feel so thankful and motivated for what’s next.”
At NBA Crossover fan fest during NBA All-Star Weekend 2024, over 20,000 fans, influencers and players got their hands on the Airless Gen1. As attendees turned to social media to share their photos and videos dribbling the ball in Indianapolis, the first online orders were also being prepared for shipping by Wilson.
“The public’s response to the Airless Gen1 has been overwhelmingly positive, and we are thrilled to be able to share this iteration of our work. One of Wilson’s core values is innovation and the belief that without risk, innovation is impossible. As we look forward to what generation two and beyond could look like for the airless ball, our goal is to keep innovating in this space and challenging the principles of how we design, manufacture and distribute.”
Video Options:
Introducing the Wilson Airless Prototype Basketball (features K.J. Martin)
The Making of the Wilson Airless Prototype Basketball (includes Nadine)
The Wilson Airless Gen1 | The Ball That Bounces Without Air
Product Landing Page:
Social Media Accounts:
Instagram: @Wilson